W
webadmin
Guest
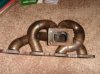
Last week we backgrounded the making of a custom turbo manifold. This week we look at the process of constructing a four cylinder manifold from heavy gauge buttweld fittings. If you have a bench grinder, hacksaw, vice and access to an experienced welder, it’s easier than you think! In the second half of this article we take a look at turbo manifold design.
Step-by-Step
Half a metre of 100mm x 12mm flat bar was purchased from a metals dealer at a cost of AUD$16. Using chalk, the shape of the exhaust manifold gasket was traced onto the bar. Because the openings in the head gasket are larger than the internal diameter of the ports, an appropriately sized washer was used to mark the port openings.
An oxy acetylene torch was used to cut out the manifold plate. The cut was made on the outside of the line so that the resulting plate is a little larger than the gasket. The holes were cut on the inside of the marked line. A local welder did all the cutting and welding – his total time was 5 hours.
The rough edge resulting from the oxy cutting was smoothed by an angle grinder. The port holes were not smoothed until the runners were welded in place, so that they could then be matched to the ports and the runner internal diameters in the one operation.
The location of the turbo relative to the head was decided by simply holding the turbo in different positions and judging clearances. From this it could be seen that the manifold runners would probably need to head upwards a little before coming down towards the turbo inlet – that way, the turbo could be kept close to the block without the runners having to bend too sharply.
The metal exhaust gasket was used whenever the spacing of the runners needed to be checked. Here the centre two runners can be seen taped together prior to welding. To allow them to nestle together, a section was cut from each 90-degree bend with a hacksaw.
A small portion of the tape was cut away to allow a tack to be made. With the pipe bends then held together, the tape could be stripped off and more tacks – and then a proper weld – made.
With the centre pipes shaped and then welded together, the outside cylinders could be organised. As can be seen here, again the head gasket is being used to determine pipe spacing. Ninety degree and a 45 degree bends are being used to form this runner, with a substantial amount of the 45-degree bend needing to be cut away. Again a hacksaw was used to do this.
Here’s what the 45-degree bend looks like when shaped to match the other runner. An oval-shaped hole was cut on the side of the runner to suit the entering pipe.
With both 45-degree bends cut to suit, and appropriate holes made in the existing runners, here’s what the assembly looked like. Note again how the exhaust manifold gasket is being used for sizing – if you buy a spare gasket and take careful under-bonnet clearance measurements, you can build the manifold without having your car off the road.
The 45-degree bends were tacked and then welded in place before they were welded to the 90-degree bends. This was done for a very important reason – it allows...
....access for an oxy cutting torch to clean-up the internal transition at the pipe junction. If the 90-degree bend had been welded to the 45-degree bend first, the welding torch would not have been able to gain access to the junction.
The rest of the runners could then be welded in place, and then welded to the manifold plate. This done, the previously cut out turbo mounting plate could be welded to the collector tube.
The welds were cleaned-up with an angle grinder spinning a multi-flap sanding disc, and a high speed electric tool using a cutting burr. A round hand file was also used.
The manifold could then be checked for turbo location.
The next step was to have the manifold sandblasted, inside and out. Externally, this removes surface scratches and sanding marks and gives a uniform finish. Internally, it helps to remove any welding dags and scale. If you chose to have the manifold internally sandblasted, you should then clean the insides very thoroughly to get rid of any blasting sand that might remain.
The manifold and turbo mounting flanges were then faced – that is, were machined flat so that good seals with the head and turbo could be gained. A local machine shop did this work. If you have this work done by a machine shop, it’s also a good time to have the manifold drilled and tapped to take a pressure tapping point and thermocouples (either one per cylinder or one just prior to the turbo).